As heat pump water heaters reach higher adoption, what do I need to know in order to properly model them?
-Hot For Heat Pump
Dear Hot For Heat Pump,
Good question! Heat pumps are getting more attention these days for both space conditioning and water heating as electrification is increasingly seen as part of the path to reducing emissions. You might have plenty of experience modeling water heaters and feel like you’re a pro with plant loops, but heat pump water heaters (HPWHs) do require some additional considerations. I’ve been modeling HPWHs for over a decade and did my thesis on modeling HPWHs with one of the first national scale analyses of their performance, so I’ve picked up a lot of tips for modeling this technology. Heat pump water heaters have been around for decades, but in the last 10-15 years multiple major water heater manufacturers have launched and refined product lines. This article focuses on modeling residential integrated HPWHs, but many of the considerations would also apply for split HPWHs or those sized for commercial buildings. A model that gives you good results for an electric resistance tank may not provide you accurate results if you just add a heat pump. To be able to do a good job modeling a HPWH, the first step is to know how the actual equipment operates. If you don’t understand how the physical equipment operates, you won’t know if your model is behaving correctly or not.
How do HPWHs work?
As the name implies, HPWHs integrate a heat pump with a water storage tank. This heat pump works like any other heat pump, pulling heat out of the ambient air and moving it into the water storage tank. While the majority of the load is met through the heat pump, the tank frequently also includes backup electric resistance element(s). While the heat pump is much more efficient, it heats the tank more slowly than the elements, so the elements tend to turn on when there are large loads. Under default controls, the HPWH will favor the heat pump, but at a certain point if the heat pump doesn’t have the capacity to provide adequate hot water the backup elements will turn on. The exact setpoint where the heat pump and element(s) turn on is based on the onboard control logic and is specific to each manufacturer. Most HPWHs also have multiple operating modes, which may disable the backup elements entirely. The control logic to use in simulation is generally derived through comparisons to measured laboratory data.
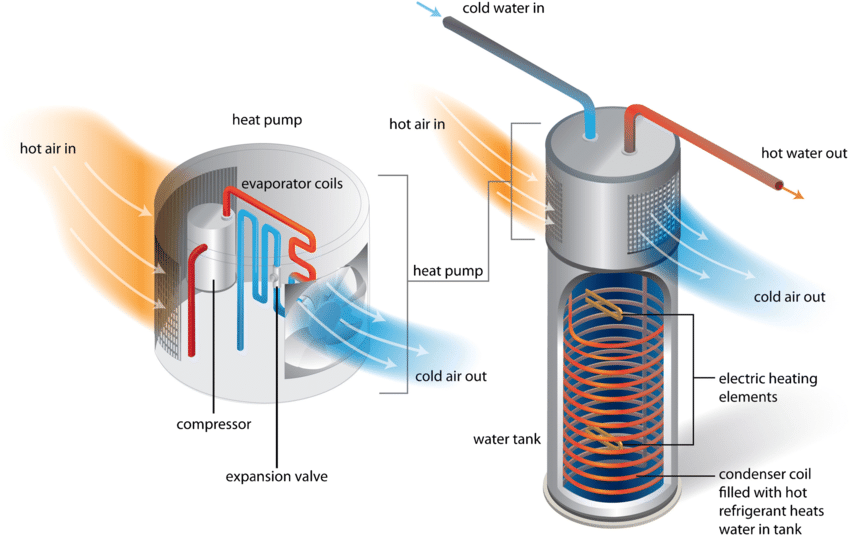
Figure 1: Schematic of a HPWH. The HP evaporator sits on top of the tank, and wrapped condenser coils transfer heat into the tank. Backup heating elements are frequently included and may trigger depending on the water heating load and operating mode. (Image by NREL.)
What additional information do I need to model a HPWH?
There are two critical pieces of information you need to model HPWHs: you need to know the performance of the heat pump under the full range of conditions and how the HPWH controls which heat source is operating. Performance maps are generally derived through detailed laboratory testing under a broad range of ambient conditions and then validated against additional data not used in the derivation. If you’re modeling residential integrated products, the EnergyPlus example files for HPWHs include a performance map derived from extensive comparisons to laboratory data. This performance map could be used for any systems with a similar heat pump (primary concern is using the same refrigerant), split or integrated. The type of refrigerant used has a large impact on the thermodynamics of the heat pump, which are captured in the performance map. Most HPWHs today use R134a as the refrigerant. However, it would not be appropriate to use with HPWHs using different refrigerant such as CO2. For the control logic, you can either derive your own based on measured data or look at what’s used in existing HPWH models to inform your setpoint and deadband assumptions. There are existing models in OpenStudio-HPXML and ResStock, tools designed to be able to model residential buildings all across the U.S., for a HPWH from a major manufacturer that you could pull control logic from. You could also look at HPWHSim, a tool designed specifically for HPWH modeling, to see what control logic they use for different products.
What else should I watch out for?
Timestep length matters much more for a HPWH than it does for gas or electric tanks. Larger timesteps have two main implications: the water draw profile may be spread out across the entire timestep and the HPWH has fewer opportunities to make a control decision. Some BEM tools have a separate timestep for the water heater to address the less frequent control decisions. EnergyPlus includes an adaptive timestep algorithm where it will take larger timesteps when nothing is happening and smaller timesteps when control decisions are being made (generally during hot water draw), but for tools that don’t, it's important to have small enough timesteps that the model can accurately figure out which heat source needs to trigger during recovery. Larger timesteps may smooth out demand for hot water such that the model uses the wrong heat source. If a large draw happens across say a 10 minute window, for example, modeling with hourly timesteps will require that same event to be evenly distributed across the whole time step. This flow rate matters because it affects the internal tank temperature dynamics. A large draw over a 10 minute window might require the backup element to turn on, but if this draw were averaged over an hour, the heat pump could keep up with the rate of demand. Shorter timesteps can avoid this problem, with 1 minute timesteps being ideal for capturing the real spikes in hot water usage, especially in residential buildings.
You also want to use a stratified tank model when modeling HPWHs rather than a mixed tank. Mixed tanks are assumed to be a single uniform temperature, while stratified tanks account for vertical differences in tank temperature. The heat pump performance depends on the temperature of water adjacent to the condenser, which is generally the bottom half of the tank. Assuming a fully mixed tank will not accurately represent the temperature of the lower half of the tank, especially during recovery from draws, which will affect the COP and capacity calculations using the performance map.
Now that you know the pitfalls you’ll encounter, you too can become an expert in HPWH modeling. Happy modeling!